December 2008 Vol. 63 No. 12
Business
Bore-Tek Overcomes Challenges, Obstacles, Tragedy
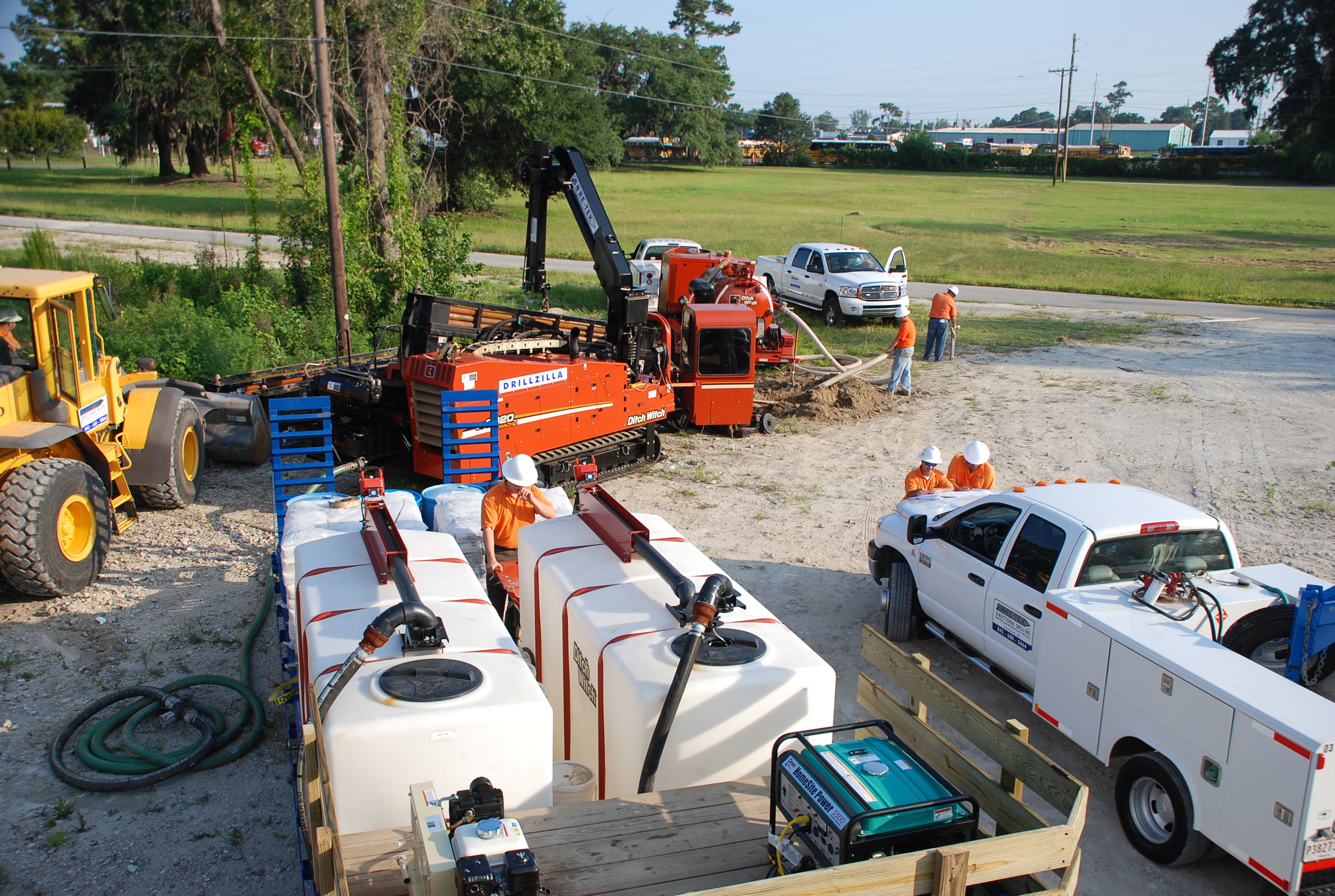
Establishing any new business is a major decision, and once the company is in operation, guiding it to success means overcoming a variety of challenges and obstacles, many of them unexpected.
Those who choose to start a utility construction firm recognize there are variables not found in other fields – the weather, permitting and regulatory issues that must be taken into account on every project.
In May 2000, three South Carolinians decided it was time to stop working for others and apply their experience and knowledge to their own directional drilling business. With one compact drilling unit, one truck and one trailer, Bryan Williams, Terry Thompson and Eric Lovell started Bore Tek Inc. in the city of Charleston.
The timing seemed right. The telecommunications building boom of the late ’90s was still under way. Construction of Level 3 Communications’ new 15,000 mile long haul network was not yet complete, and there appeared to be plenty of subcontracting work for small horizontal directional drilling (HDD) companies.
Getting started
However, getting started wasn’t easy, recalls Thompson, current Bore-Tek president.
“From the beginning,” he says, “finding financing for our business was difficult. We had no track record. But we were determined. The drilling unit we wanted – a Ditch Witch Jet Trac JT1720 – was for us the biggest initial investment. Our equipment dealer – Ditch Witch of the Carolinas – recognized our commitment and took a risk by internally financing the drilling unit’s purchase.”
A month later the new company got it’s first HDD project and, with its one employee, traveled to Charlotte, NC.
The job did not go well.
“We were booted out of the state after we released drilling fluid collected from the job site at a location where we were unaware that dumping was prohibited,” says Thompson. “Then on our second job in Atlanta, we drilled into solid rock, destroying our only drill bit. Our first year was very discouraging.”
Still, the three persisted, taking projects in Mississippi, Alabama and Florida with what Thompson describes as “minimal” success.
“Leaving damaged utilities in our wake, we knew it was time to regroup,” he continues. “It was time to ‘do or die.’ Money was so tight, we sometimes slept in our trucks. We challenged ourselves to learn from our mistakes and not be discouraged by them. Knowing there was demand for work in our industry, we were determined to put ourselves in a position to be successful. We really had no option but to make the business succeed – everything we had was invested in it.”
Of course, Bore Tek wasn’t the only HDD subcontractor with problems during that time. Inexperienced “cowboy” drillers still are remembered for careless, sloppy work that gave the HDD industry a bad name that lingers today.
However, Williams, Thompson, and Lovell never fit the cowboy category. Their goal was to provide quality work, and they worked hard to overcome the early setbacks and improve their drilling operations. With greater understanding of the capabilities of its equipment and more experience in the field, successful installations dramatically increased. The Bore Tek owners began introducing themselves to general contractors, engineering firms and municipalities. The promoted Bore Tek, its services and explained how they could assist on projects that required horizontal directional drilling.
But just as the company had prepared itself for more work, the telecom building boom went bust, and the HDD industry fell into the most severe depression of its relatively short life.
Smart move
Fortunately, aware that telecommunications projects were declining, Bore Tek shifted their focus to the water and sewer markets before the bottom fell out of the telecom market, leaving hundreds of HDD specialists with no work and without experience in other markets.
“By earning the confidence of several local general contractors, we began to fill a niche market in water and sewer,” Thompson said. ‘”We ventured into multi duct bores, ductile iron bores and grade bores. Realizing the increasing demand for larger bore projects, we purchased a Ditch Witch JT4020 with 40,000 pounds of pullback capability.”
As the water and sewer business grew, in 2005 an even larger JT7020 model was leased, then purchased. The bigger, more powerful drilling unit allowed Bore Tek to bid projects that contractors who had done only telecom work with smaller machines could not do. Those contractors remained mired in the industry’s recession and were unable to purchase or lease larger equipment. As many HDD contractors struggled or went out of business, Bore Tek not only survived, but grew. As the company’s workload continued to increase, Bore Tek ordered a new 80,000 pound pullback Ditch Witch JT8020, the model that had replaced the JT7020 in the Ditch Witch HDD lineup.
By 2007, the Bore Tek partners were ready to take on the biggest project in the company’s history, installing 15,200 linear feet of 24 inch diameter fusible PVC pipe to expand water services to the rural sea island communities of Johns Island, Kiawah Island and Seabrook Island, just south of Charleston.
“The material costs alone were larger than our previous year’s revenues,” recalls Thompson.
Big risk, big reward
The project owner was the St. John Water Company. The general contractor for segments of the project that included directional drilling was R. H. Moore, Murrells Inlet, SC, and engineering was provided by BP Barber & Associates, Columbia, SC. R. H. Moore hired Bore Tek for the segments to be installed by directional drilling. The 24 inch diameter, DR25 fusible PVC pipe was manufactured by Underground Solutions. Most of the route of the directionally drilled segment was along River Road, a designated scenic highway.
Environmental issues were a primary factor in selecting HDD to install the pipe along River Road.
Frank Iwanicki of BP Barber explains that most of the roadway is lined with large live oak trees, some with trunk diameters of 80 inches. All trees of trunk diameters of six inches or larger along the road are protected. In addition, numerous wetlands, marshlands and tide influenced crossings were necessary, and directional drilling was determined to be the best method to protect the environment.
Iwanicki explains that fusible PVC was selected over HDPE for the HDD portion of the project because it could be installed in a smaller diameter hole.
“Horizontal directional drilling for the installation of fusible PVC pipe enabled the project to be completed in a very short time frame, under budget, while preserving the rural character of River Road and providing a much needed alternate water supply, ” adds Iwanicki.
Not long after Bore Tek crews started work on the Johns Island project, the company’s new Ditch Witch JT8020 horizontal drilling unit arrived. The small JT1720 that had served the company since its first HDD job was sold to another contractor. With machines with pullback forces of 40,000, 70,000 and 80,000 pounds, Bore Tek was firmly positioned to service the water and sewer markets that had become the basis for its success and growth. The new machine would be immediately put to work on the Johns Island project.
“We give our equipment names,” says Thompson, “and late in the day the JT8020 arrived, Bryan Williams suggested ‘Drillzilla.’ It was our biggest, most powerful HDD unit and the play on ‘Godzilla’ was a natural.”
Tragic turn
The following morning, Williams was killed in a traffic accident.
“The accident occurred less than a mile from where the crew was to make a bore with the new machine,” says Thompson. “Naming the new machine was one of the last acts he made for our company. The machine – and the name he gave it – reminds us of Bryan and what he meant to the company and to us personally.”
Needless to say, the next few weeks were a hardship for the crew emotionally. “Ironically,” says Thompson, “one of bores remaining to be done on the project was at the intersection where Bryan’s accident had occurred.”
Ultimately the project required 23 bores ranging in length from 90 to 1,350 feet with the average being approximately 600 feet. Depths were from 6 to 21 feet. All bores were made with the JT7020 and JT8020 machines.
The narrow, two lane road bordered by the huge trees allowed little room to work, but the project was completed without ever closing the road to traffic, except for brief periods while equipment was being moved.
Soil conditions varied from course sand to marine clay and the pilot holes was nine inches in diameter. Two back reaming passes were required to enlarge the pilot hole to 38 inches for product pull in.
The final phase of this project included 5,208 feet of pipe installed in nine separate bores.
“This segment was completed in 30 days, which ended our portion of the project three days early,” says Thompson. “This level of production was not accomplished without overcoming obstacles that included sink holes and breaking of the shaft of the reamer.”
Bore Tek drilling crews remain busy today on a variety of projects.
“We now concentrate on competitively bidding and successfully completing projects in North and South Carolina and Georgia, mostly within a two hundred mile radius of our home base in Charleston,” says Thompson. “Hard work and team effort have earned our reputation as a company being able to attempt most any bore project and find a way to get it done, earning the respect of local municipalities, engineering firms, and general contractors. We have successfully executed shots as short as 50 feet for 1 to 1 1/4 inch conduit installations to distances of 1,350 feet of 24 inch pipe and 1,435 feet of 20 inch pipe.
HDD Contractor: Bore-Tek, (843) 688-5864, www.boretekinc.com
HDD/vacuum excavator equipment: Ditch Witch, (800) 654-6481, www.ditchwitch.com
Fused PVC pipe: Underground Solutions, (858) 679-9551, www.undergroundsolutions.com
Engineering: BP Barber & Associates, (803) 254-4400, www.bpbarber.com
Comments